Novel approach reduces alloy microstructure prediction from years to minutes
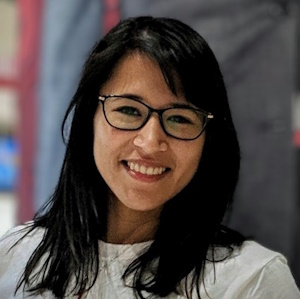
Gaby Clark
scientific editor

Andrew Zinin
lead editor

For thousands of years, humans have combined metals to collectively harness properties found in individual components, producing such practical materials as bronze, brass and, more recently, steel. However, predicting the exact microstructures underpinning these alloys to understand how specific properties of the constituent materials may manifest across scales is still a complex mystery researchers are working to solve. Now, thanks to a team based in Japan, that work could take minutes instead of years.
The researchers developed a new computational approach, the details of which were published on July 15 in , that predict features of the microstructures formed when materials are combined. The new model streamlines older approaches so efficiently that the team was able to predict the microstructures of an alloy with more than 10 components in five minutes. Previously, such calculations took two years.
"When developing new materials, merely optimizing composition is insufficient, as material properties depend significantly on both the average composition and microstructure," said co-author Shoichi Hirosawa, professor, Faculty of Engineering Science, YOKOHAMA National University. "This microstructure is characterized by the arrangement and size of grains and phases, with differences in concentration, crystal structure and other features."
Alloy microstructure predictions save money and time because researchers don't need to go through the trials and errors of physically combining materials without knowing how the materials might work together. Existing computational approaches are still costly in terms of time and resources, though, as they depend on implicit functions, or solving for equations that relate to variables rather than solving the variables directly since the parameters are unknown. Once implicit functions are determined, additional calculations are still needed to predict the specific conditions of microstructures.
"Predicting microstructure of alloys traditionally requires solving implicit functions, making the computation time impractically long," said corresponding author Takumi Morino, doctoral student in the Graduate School of Engineering Science, Yokohama National University. "To overcome this problem, we reformulated the implicit functions into explicit forms, enabling a novel approach for predicting the microstructure of multicomponent alloys."
Imagine a simple mathematical equation, where the variable "y" is equal to another unknown variable, "x," plus a known number, like two. The "y" variable is dependent on whatever "x" is, but it's isolated in the equation, so the problem can be worked through to isolate "x"—in this case, if y=x+2, then x=y-2.
Both variables can be directly expressed by the equation, meaning the isolated variable is a function of the other—an explicit function. However, if the variables are not and cannot be isolated in the equation describing their relationship—like "x squared" plus "y squared" plus two equals zero—then both sides of the equation need to be processed to understand how the variables influence one another.
Boiled down, this series of calculations—known as an implicit function—determines the rate of change for the whole system if either variable changes. For predicting microstructures, the implicit function elucidates the equilibrium arrangement and distribution of atoms at the microscopic level.
In previous approaches, researchers had to calculate how phases may reach equilibrium implicit functions at every point in space and time during a simulation. This leads to billions of evaluations of phase diagram—a graph that details a system's physical state of gas, liquid or solid at specific temperature and pressure points. As the number of elements used in an alloy increases, the computational complexity grows exponentially, leading to what is known as the "curse of dimensionality."
"Our new model dramatically reduces this burden by reformulating the problem, avoiding repeated phase diagram calculations and overcoming the curse of dimensionality," said co-author Machiko Ode, senior researcher at the National Institute for Materials Science.
The approach redefines two of the broad settings—how constituents may diffuse and the conditions to reach internal equilibrium—and formulates them into what's called an "evolution equation." The researchers can assess how a system changes over time, which considers diffusion and equilibrium, without calculating every potential eventuality at every single time point.
"This is a generalized model that performs rapid and accurate calculations of the solidification of aluminum, nickel and iron systems and more," Hirosawa said. "Moreover, we successfully performed a simulation of alloy microstructures containing a record-high 20 elements."
Next, the researchers said they plan to incorporate atomic vacancies—holes in the crystal lattice of atoms comprising a material—into the model, broadening its application to steels.
"Ultimately, our goal is to establish a universal framework for microstructure prediction that is applicable to any alloy system, thereby transforming materials development from a trial-and-error approach into a streamlined, digitally driven process," Morino said.
More information: Takumi Morino et al, An explicit integration approach for predicting the microstructures of multicomponent alloys, Nature Communications (2025).
Journal information: Nature Communications
Provided by Yokohama National University